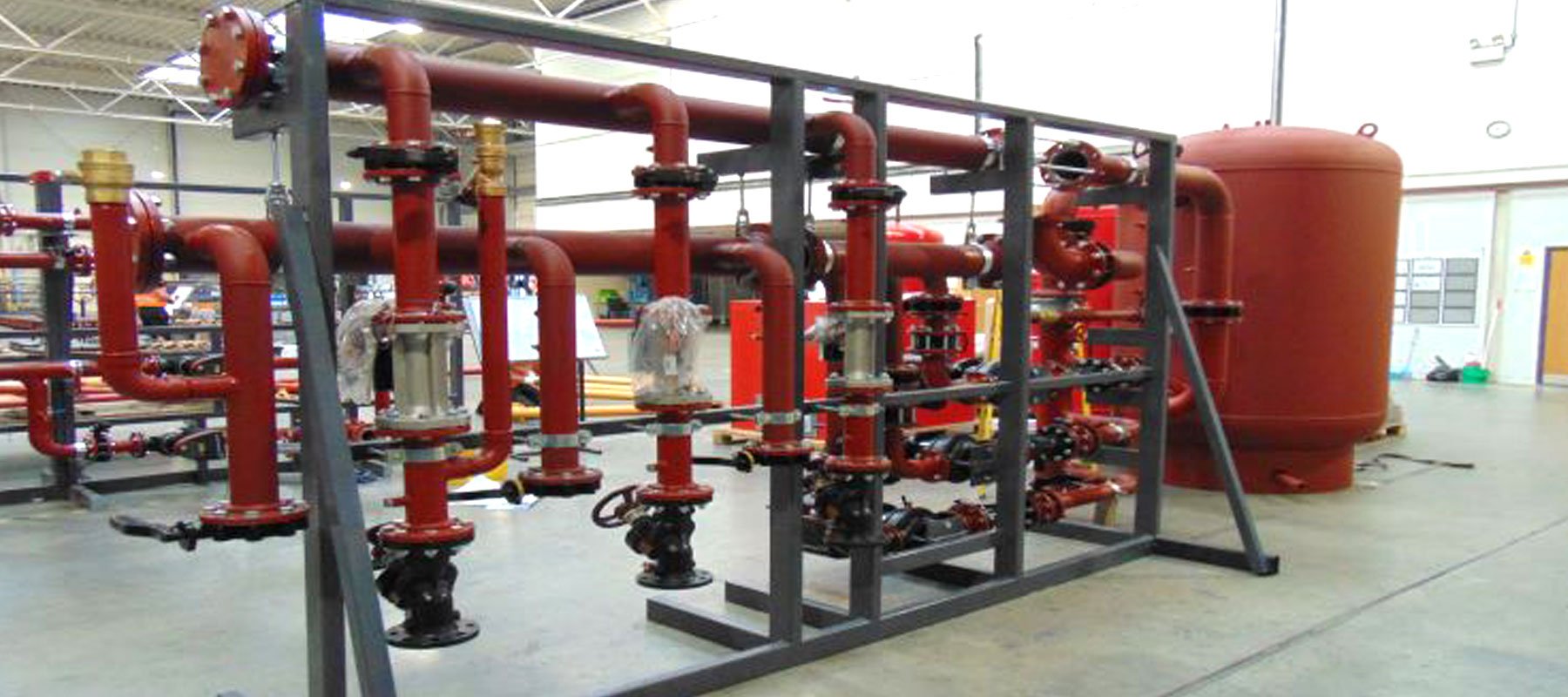
Blackberry Hill Vistry Partnerships
Installation: Offsite-fabricated packaged plant solution involving Remeha R-Gen CHP 20/44, 2 x Remeha Gas 610-10 Eco Pro boilers, and 2 x buffer vessels.
Working in partnership with Homes England, Bristol City Council and Sovereign Housing Association, Vistry Partnership has transformed the former Blackberry Hill Hospital site in Fishponds, creating 346 high-quality new homes (including 100 affordable homes).
As well as new homes, the project has also created retail and start-up business units, a community building and extensive green spaces for the community to enjoy.
Offsite fabrication has been central to the design with many of the new homes being built via an innovative modern method of construction – the SIG I-house – which means that the homes can be built to high standards but in a much quicker timeframe than traditional construction methods.
A similar approach was adopted when designing the heating and hot water services. Heat experts Baxi Commercial Solutions were brought in to design a bespoke packaged plant solution that would meet the unique project requirements at Blackberry Hill within the design parameters.
David Cowling, Project Manager at Vistry Energy, explained:
“When evaluating the options for this project, we had to rule out both ground source and air source heat pumps due to insufficient external space – they simply weren’t feasible. Instead, an energy-efficient CHP and boiler system was deemed the better option, easy to run and simultaneously providing heat and onsite electricity at lower prices.”
A Remeha R-Gen Combined Heat and Power (CHP) 20/44 unit, two Remeha Gas 610-10 Eco Pro boilers and two buffer vessels were selected to serve the four district heat circuits feeding the original Blackberry Hill buildings, a converted chapel and several new blocks on the site.
“We faced a number of challenges on this project,” said David. “First, the ability to fit the central plant into the extremely tight space within the plant room. There was also the matter of the listed status of the building which ruled out any changes to the exterior fabric and meant that all equipment needed to fit through the existing window louvres.
“The advantage of working with Baxi Commercial Solutions was that they were not only able to supply all the equipment but to design and produce a quality packaged solution offsite that would address and overcome these restrictions,” he added.
Baxi’s dedicated Packaged Solutions team proposed producing tailor-made skids with pump sets and fully insulated prefabricated pipework, using specialist equipment design to achieve the compact footprint that the project required. Working with Vistry Energy, the team prepared the layouts and schematic 3D drawings to reach a final design that met all the site needs.
Once the system had been fully assembled in the factory and end-of-line testing had been completed, the Vistry team were able to inspect the modules before Baxi reassembled them in the Blackberry Hill plant room.
Skids are similar to plant rooms, having all the equipment without the walls. At Blackberry Hill, the skids connect onto two prefabricated frames accommodating the pumps and high-level pipework that are positioned against the walls. Two buffer vessels are sited at the opposite end of the plant room.
“Space constraints aside, using an offsite-fabricated packaged plant solution made the installation process faster, easier and, ultimately, safer,” said David. “It also meant that fewer workers were required on site at a time when Covid safety measures were still in place. A further benefit was that it removed the need for onsite hot works, such as welding, which greatly improved onsite safety.”
With the system fully operational, the Vistry Group are pleased with the outcome. “It’s a really good job,” said David. “It would have been extremely challenging to have attempted to do this project onsite. The Baxi Packaged Solutions team were great and made the whole project so much easier. We are very happy with the solution which is running extremely well.”
Baxi Packaged Solutions
In 2017 Baxi acquired Packaged Plant Solutions, since then we’ve transitioned to Baxi as our lead customer facing brand and moved manufacturing from Milton Keynes to Preston.
Related Articles
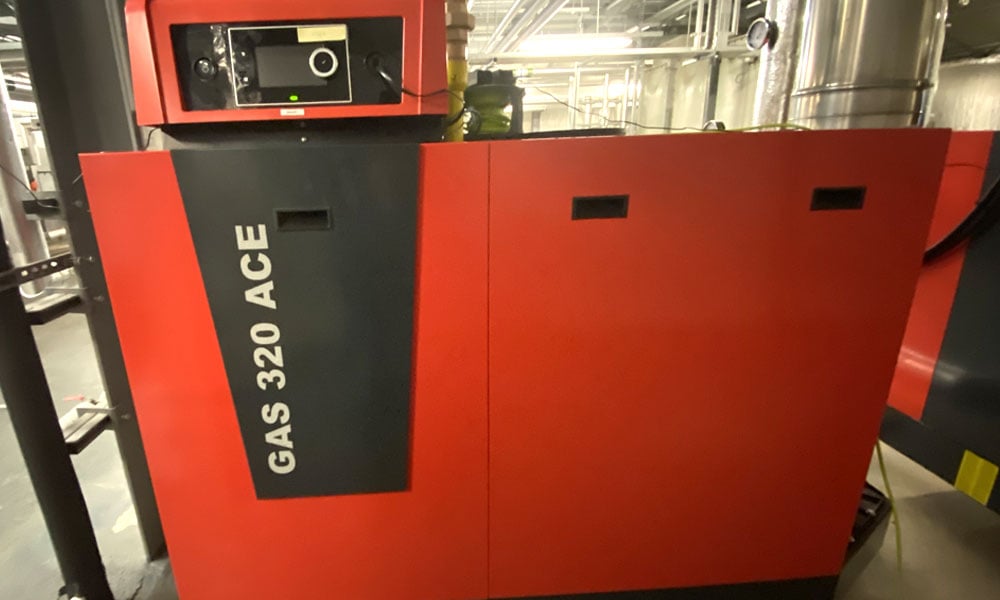
Commercial
Virgin Money
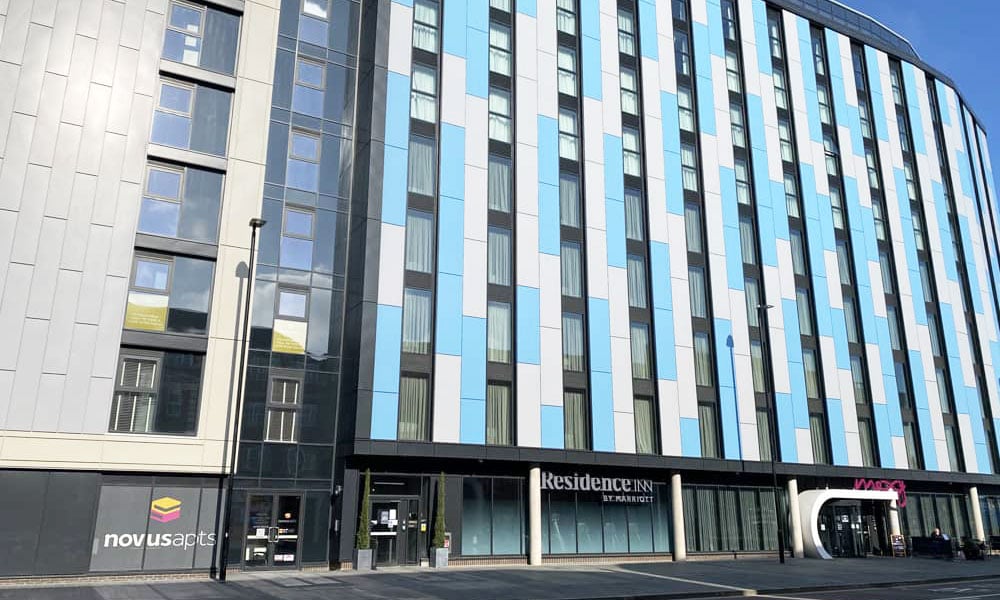
Commercial
Marriot International
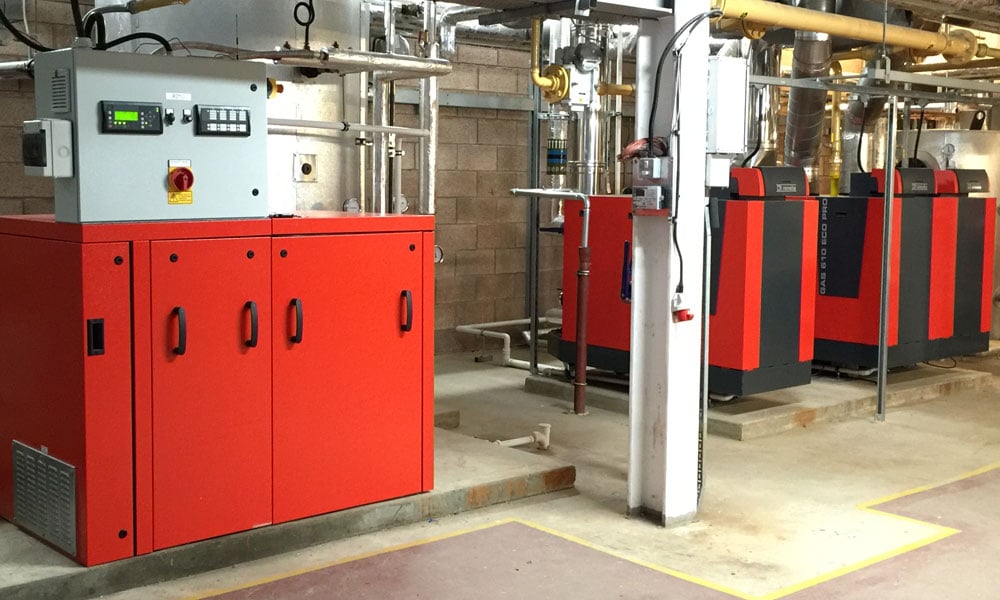
Leisure
Penrith Leisure Centre
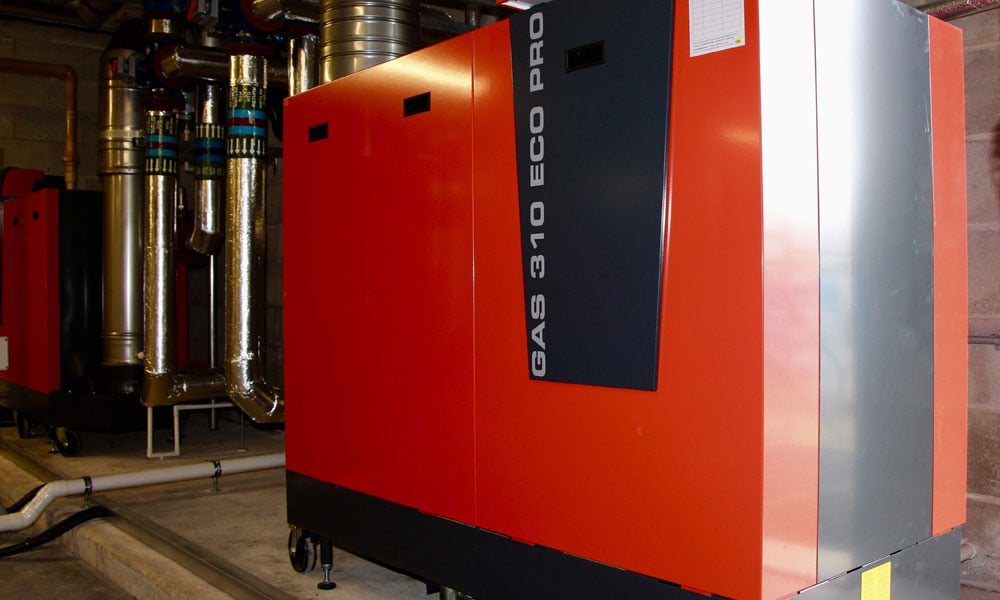
Leisure
Halewood Health and Fitness Club
About Remeha
Our dedicated experts and comprehensive project approach support you from concept to commission to achieve your project goals.